Understanding the Importance of Phosphating Plants in the Automotive Industry
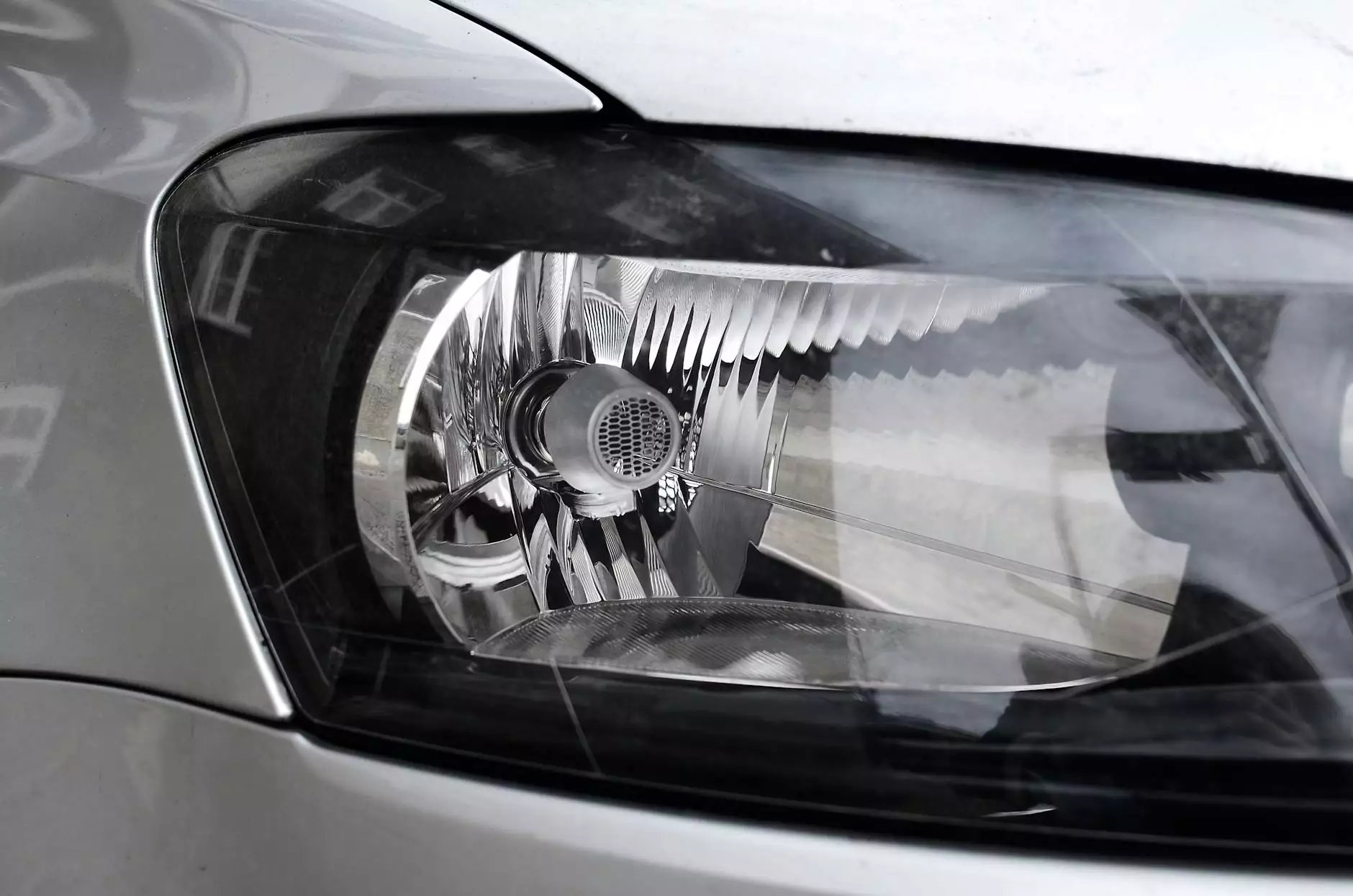
The automotive industry is one of the most significant sectors globally, characterized by its constant evolution and reliance on advanced technologies. Among the crucial processes that ensure the longevity and durability of automotive components is the treatment of surfaces through phosphating. This article delves deep into phosphating plants, exploring their role, processes involved, benefits, and much more.
What is a Phosphating Plant?
A phosphating plant is a specialized facility designed to carry out the phosphating process, an essential pre-treatment step before painting and coating metal surfaces. Phosphating involves applying a phosphate conversion coating to metal substrates, which enhances corrosion resistance and provides a good surface for subsequent coatings. It is particularly vital in the automotive, aviation, and military sectors due to the rigorous demands for strength and durability in these applications.
How Does the Phosphating Process Work?
The phosphating process can be broken down into several key stages:
- Pre-cleaning: This initial step involves removing contaminants such as oils, greases, and dirt from the metal surface. Methods typically used include chemical cleaning agents, ultrasonic cleaning, or sandblasting.
- Phosphating: The cleaned metal is immersed in a solution containing phosphates, usually zinc or manganese-based. This chemical reaction creates a layer of insoluble phosphate crystals on the surface.
- Rinsing: After phosphating, the parts are thoroughly rinsed to remove any residual chemicals.
- Drying: The rinsed pieces are then dried using hot air or drying ovens to eliminate moisture that could affect the coating process.
- Post-treatment: Sometimes, a post-treatment step involves applying a sealant or oil to enhance the protective properties of the phosphated surface and improve paint adhesion.
The Different Types of Phosphating Processes
Phosphating technologies can vary based on the type of phosphate used and the specific requirements of the applications. The most common types of phosphating include:
- Zinc Phosphating: Widely used in the automotive industry due to its excellent corrosion resistance.
- Manganese Phosphating: Known for its effectiveness in providing a good surface for oils and other coatings.
- Iron Phosphating: Used primarily for light-duty applications where corrosion resistance is less critical.
Benefits of Phosphating in the Automotive Industry
The adoption of phosphating processes in automotive manufacturing offers numerous advantages:
1. Corrosion Resistance
One of the most significant benefits of phosphating is its ability to create a protective layer that minimizes the risk of corrosion. The automotive industry requires components to withstand harsh environmental conditions, making effective corrosion protection essential.
2. Enhanced Adhesion of Paints and Coatings
Phosphated surfaces provide an improved texture for the adhesion of paints and other surface coatings. This is crucial for the visual appeal and lifetime durability of the vehicle’s finish.
3. Cost-Effectiveness
Implementing a phosphating plant can be a cost-effective solution in the long run. By using phosphating before painting, manufacturers can reduce paint failure rates, thereby lowering warranty costs and enhancing customer satisfaction.
4. Improved Wear Resistance
In addition to corrosion resistance, phosphating treatments can enhance the wear resistance of components, ensuring that they perform effectively over extended periods of use.
5. Environmentally Friendly
Many modern phosphating processes use less harmful chemicals than previous methods. This shift is not only beneficial for the environment but also helps manufacturers comply with stringent regulatory standards.
Implementing Efficient Phosphating Plants
Building and operating an efficient phosphating plant involves several considerations to maximize productivity and ensure quality:
1. Selecting the Right Technology
Choosing the appropriate phosphating technology based on the specific needs of the automotive parts being treated is paramount. Factors like the substrate material, desired coating thickness, and specific performance requirements need to be evaluated.
2. Automation and Control Systems
To achieve consistency and high quality in the phosphating process, many manufacturers are adopting automated systems. These systems can monitor and adjust variables such as temperature, bath concentration, and processing times in real-time.
3. Regular Maintenance and Monitoring
Maintaining the phosphating equipment and process parameters is crucial for the longevity and effectiveness of the plant. Routine checks and balances can help in identifying issues before they turn into costly problems.
Challenges in Phosphating
While the phosphating process offers numerous advantages, it is not without its challenges:
1. Chemical Management
Proper handling and disposal of chemicals used in phosphating processes are essential to minimize environmental impacts. This requires stringent control measures in place.
2. Consistency in Coating Quality
Achieving a uniform coating across all components can be challenging, particularly with varying shapes and sizes. Continuous monitoring and adjustments are necessary to maintain quality standards.
3. Investment Costs
Setting up a phosphating plant requires significant investment in technology, equipment, and personnel training, which can be a barrier for some companies.
Future Trends in Phosphating
As the automotive industry continues to evolve, so too do the technologies and processes related to phosphating. Some of the future trends include:
1. Sustainable Phosphating Solutions
With increasing environmental regulations, future phosphating technologies will likely focus on reducing waste, minimizing energy consumption, and utilizing less hazardous materials.
2. Advanced Coating Techniques
Research is ongoing into new coating methods that could supersede traditional phosphating, offering even better performance for automotive applications.
3. Integration with Industry 4.0
As more manufacturing processes incorporate smart technologies, phosphating plants will likely adopt IoT (Internet of Things) solutions to track and optimize operations in real-time.
Conclusion
In summary, phosphating plants play a vital role in the automotive industry, offering enhanced corrosion resistance, improved paint adhesion, and overall increased component longevity. As technology progresses, these facilities will continue to evolve, addressing challenges and embracing innovative solutions for a sustainable future. The benefits of investing in sophisticated phosphating processes far outweigh the challenges, reinforcing the importance of this key technology in automotive manufacturing.
With the right implementation and continuous improvement, companies like AutoCoat India can not only meet but exceed the expectations of their customers by delivering high-quality, durable automotive products.